CERAMIC EXTRUSION DIE INSERTS
International Syalons manufacture silicon nitride and sialon advanced ceramic extrusion and drawing die inserts. These are used for the extrusion and drawing of copper, brass and nimonic alloys in the metal forming industry. Sialons are ceramic alloys of silicon nitride and are known for their excellent wear properties, including high strength, hardness and toughness, and thermal and chemical stability.
The metal forming processes of extrusion and drawing involves the forcing of a hot metal through a die typically to form an extruded bar, tube, or wire. During this process the drawing die is subjected to extremely demanding conditions. The die must retain high hot hardness, be strong and tough, thermal shock resistant, and chemically stable.
For the extrusion and drawing of copper, brass and nimonic alloys the die has traditionally been manufactured in steel. However, steel dies are not ideal as they can give a poor surface finish and have a short die life.
To try to eliminate these problems with metal dies, advanced ceramic dies have been investigated. One the most promising of the ceramic die materials has been sialon (or silicon nitride).
Syalon 101 possesses a number of properties which make it an excellent candidate for extrusion dies. These include high hot hardness, strength and toughness, excellent thermal properties particularly thermal shock resistance, chemical stability and good frictional properties. Also, since sialon and silicon nitride materials do not contain a metallic phase, die pick-up can be eliminated, which results in improved continuity of the extrusion process, enhanced surface finish of the product, reduced scrap rates and increased productivity.
When extruding nimonic alloys, Syalon 101 dies last up to 120 times longer than steel dies. For extruding brass, Syalon 101 dies extruded 250 tons of brass compared to 100 tons through conventional dies. For copper, Syalon 101 extruded 75 tons compared to 40 tons for a conventional die.
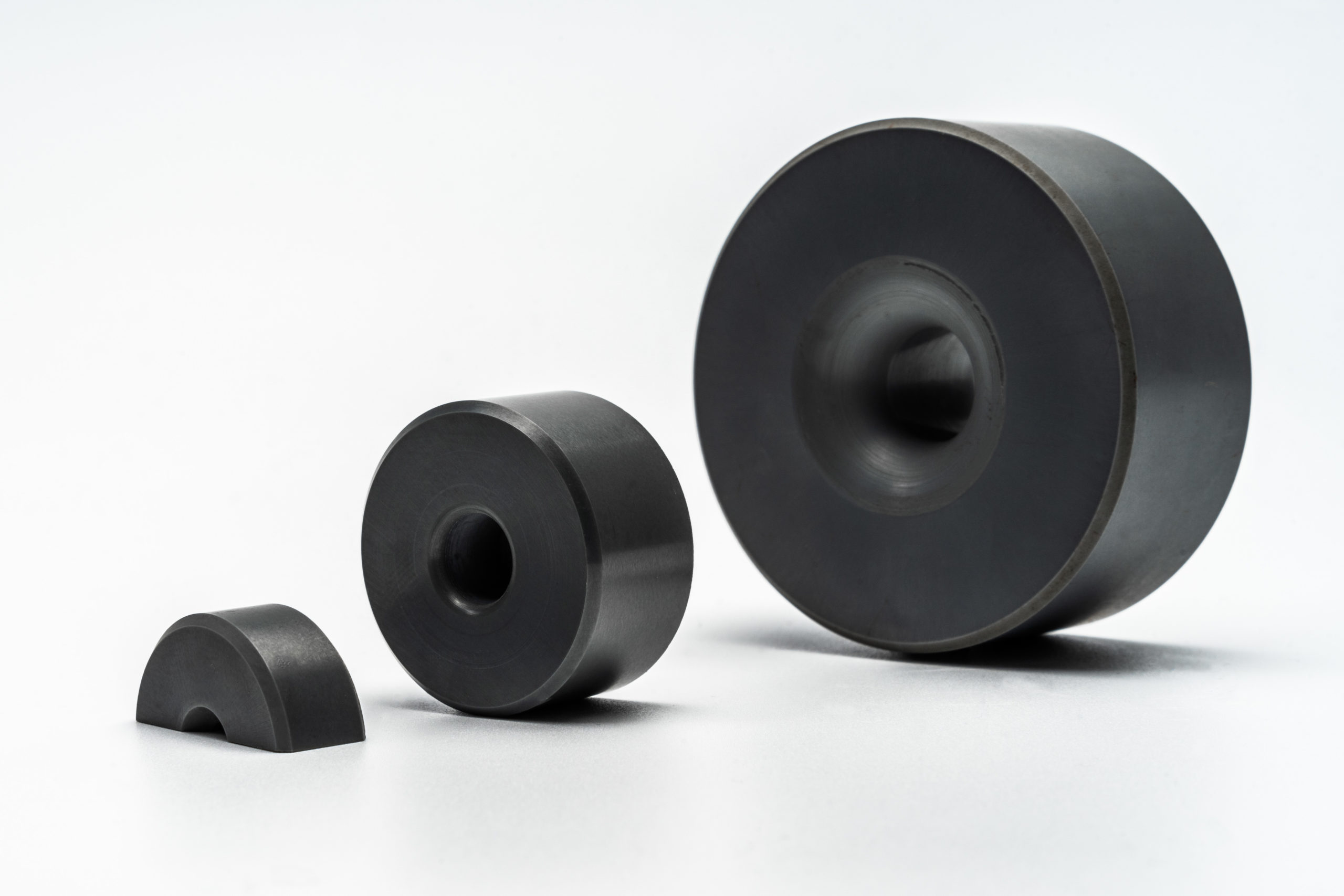
Extrusion and drawing dies are also available in an advanced ceramic which uniquely is electrically conducting. This material is Syalon 501, a composite sialon ceramic. Being electrically conductive, Syalon 501 can be electro-discharge machined (EDM) which allows complex die profiles to be formed economically. Syalon 501, like Syalon 101, possesses the excellent wear resistant properties required of extrusion and drawing dies.
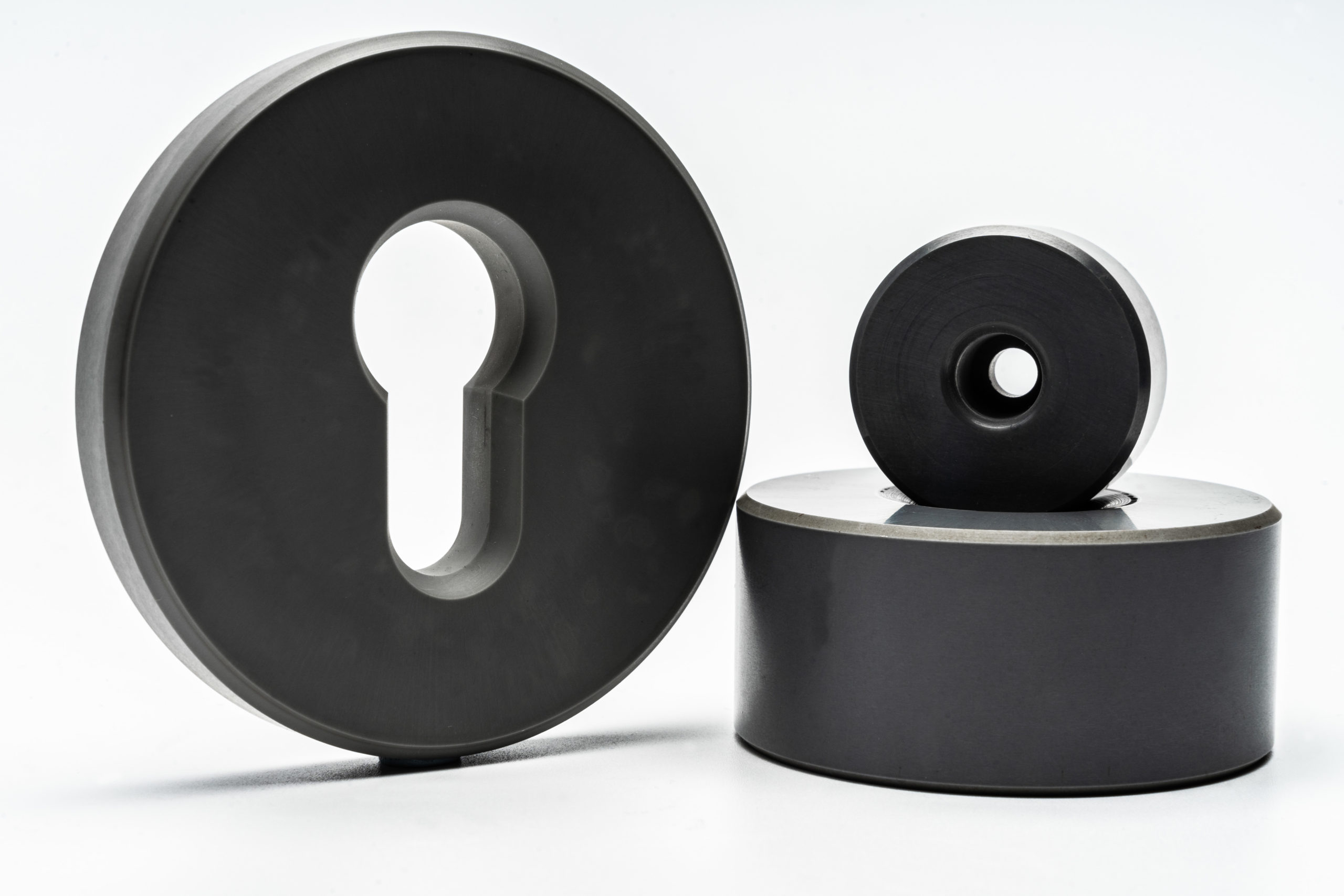
The successful integration of advanced technical ceramics into engineering systems requires close collaboration between you, the end-user, and ourselves, the material manufacturer. Please call +44(0)191 2951010 or email for an initial consultation with our technical sales team, or send us a Request for Quote.
Download our Extrusion Dies brochure or Metal Forming Applications guide for more details.
For advice on using our sialon inserts for Direct Brass Extrusion, please download our User Guide.
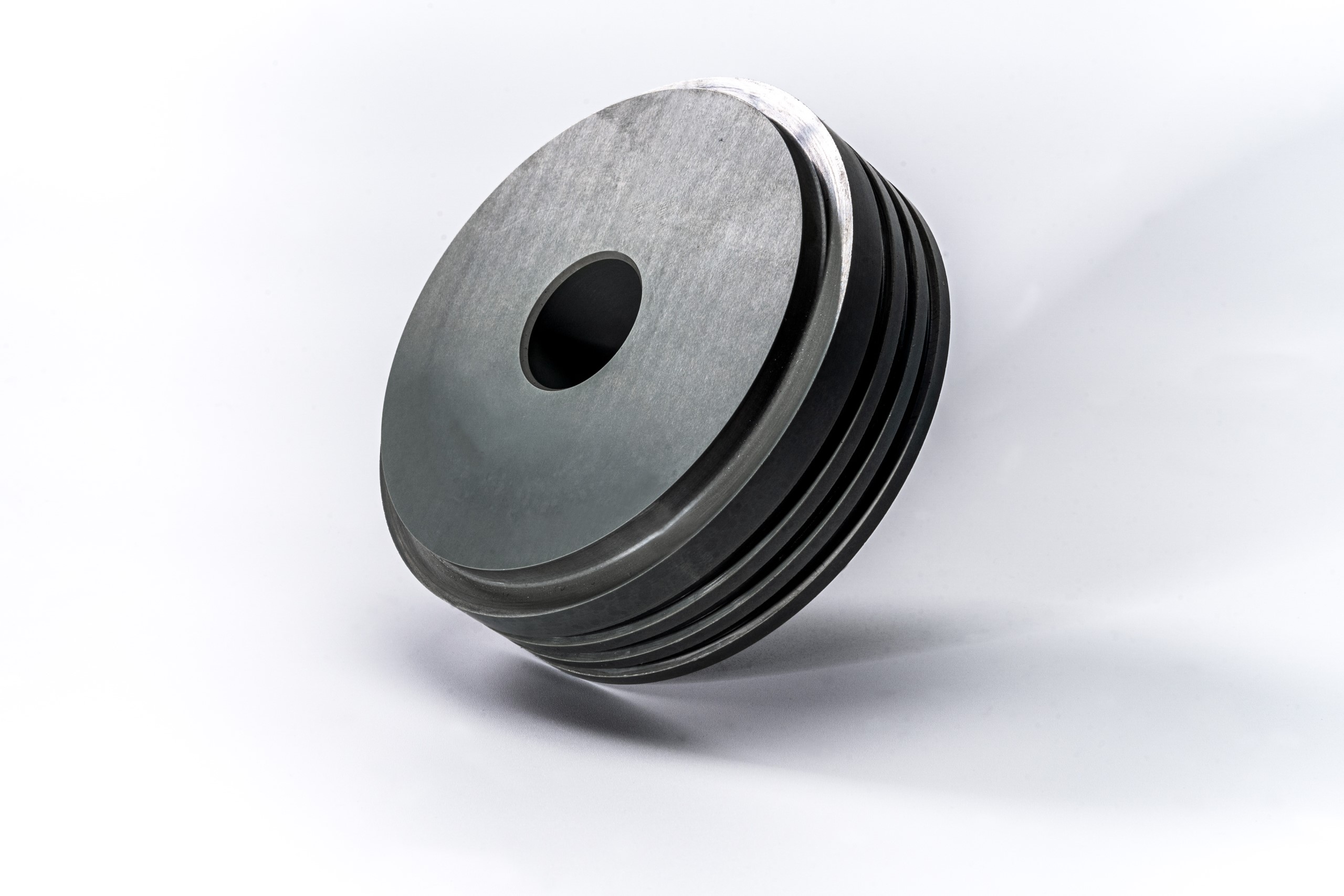
Syalon 101 is a grade of sialon which offers the best general combination of properties. These include high strength, hardness and toughness as well as excellent corrosion resistance.
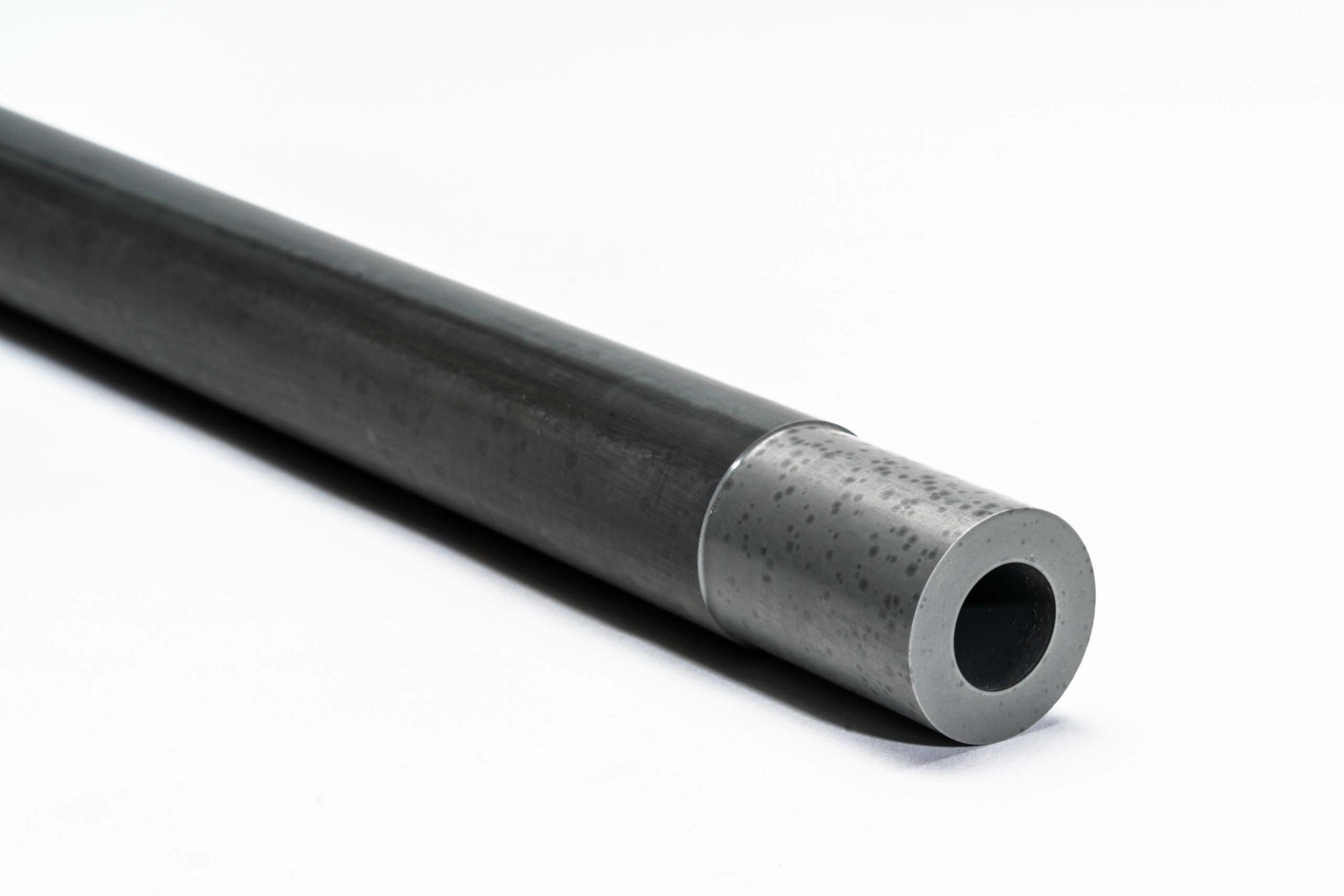
Syalon 050 is suited to wear and high temperature applications. It has extreme hardness combined with high strength and can be used in applications up to 1400°C in air.
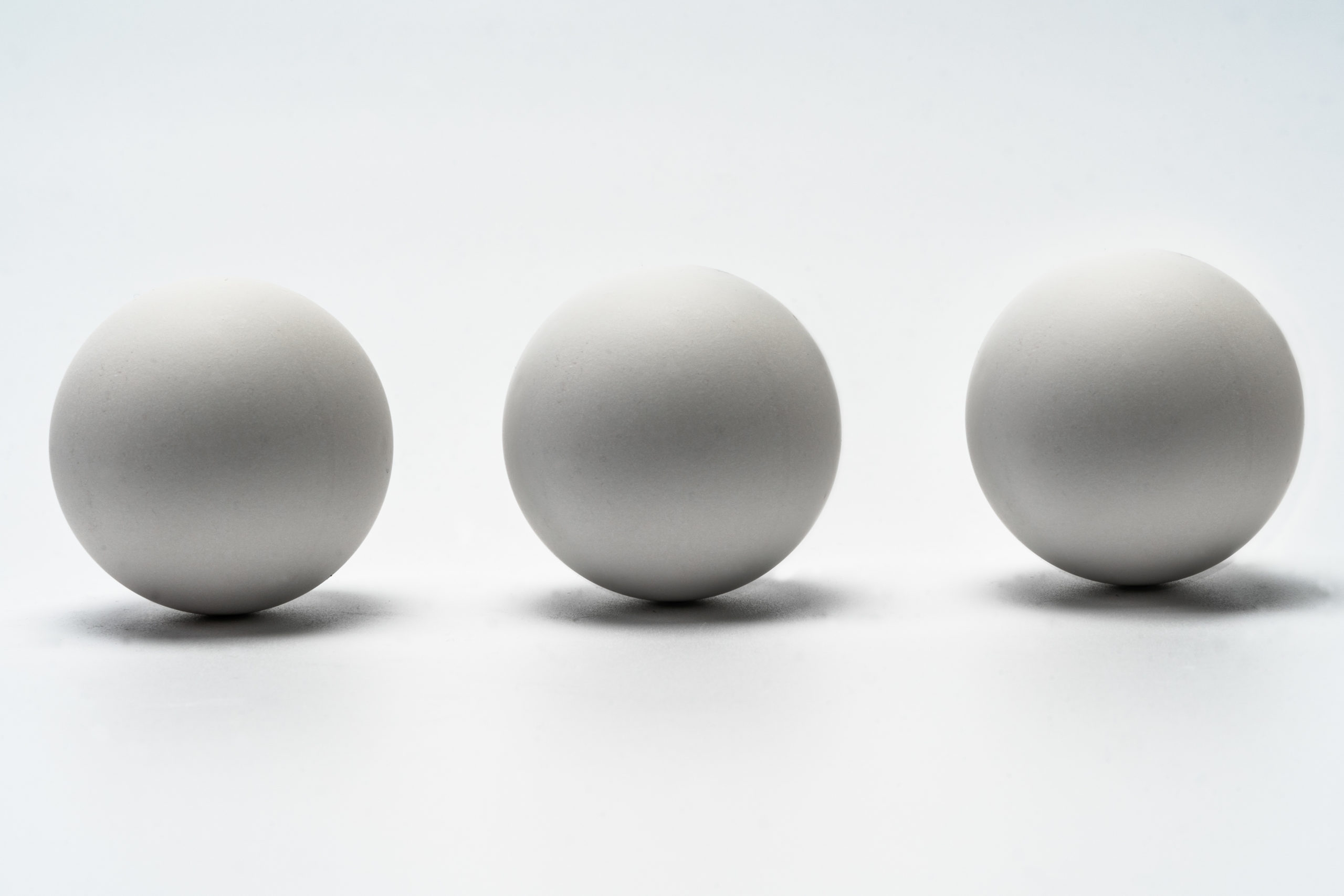
Syalon 110 is silicon nitride-boron nitride composite, offering high temperature corrosion resistance in challenging molten metal handling applications.
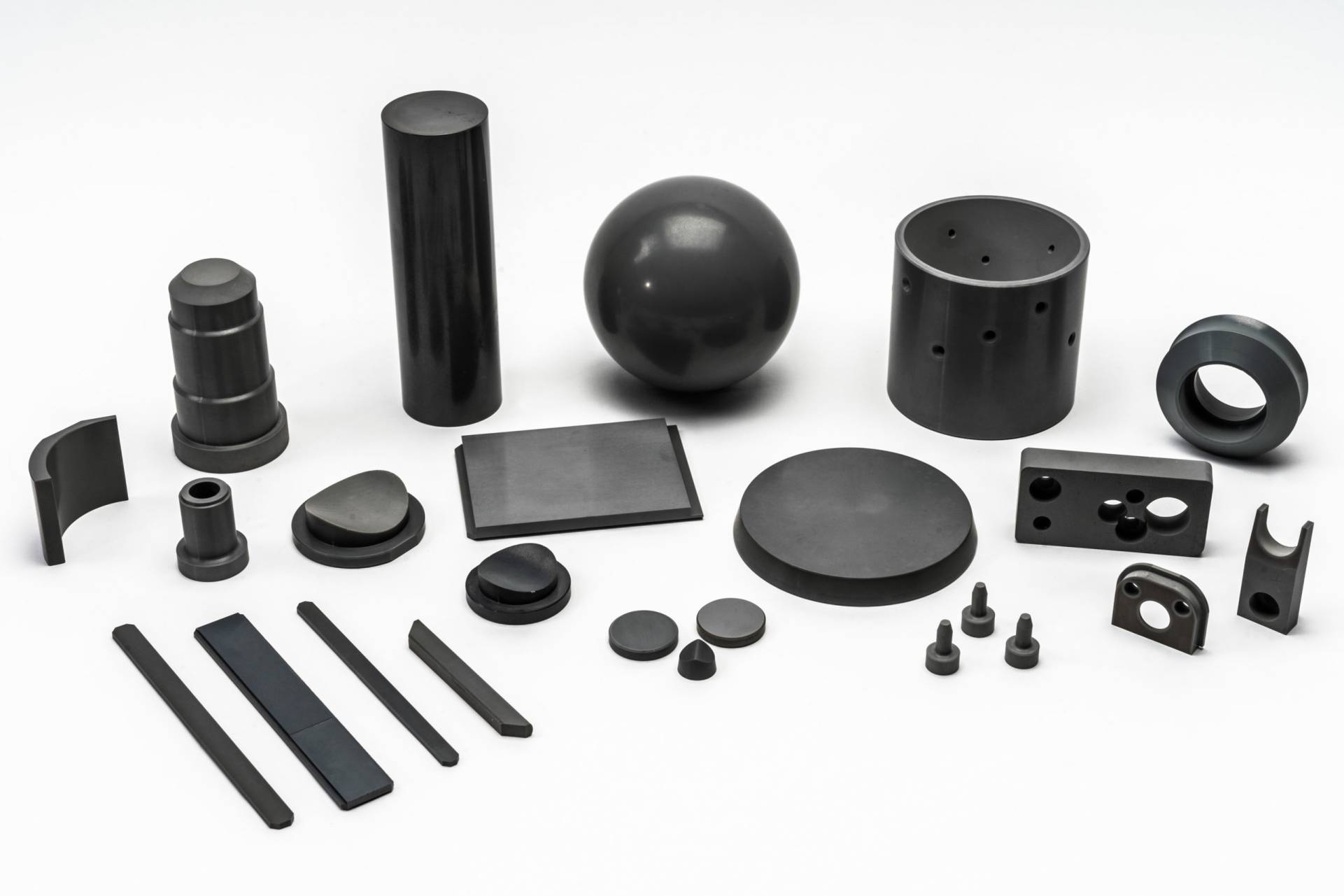