Light metals are those which have a relatively low density. Some of the most commonly used light metals are aluminium, titanium, and magnesium.
When it comes to light metal forming there are a number of shaping techniques to choose from, each of which offers their own benefits and limitations. Each technique is suited to one or more of a range of applications and different types of metal.
Metal forming processes are a critical part of our industrial society, without them, day to day life would be substantially impacted. The products and components which are created by metal forming techniques are employed in a range of applications from heavy machinery, household consumable products, artificial intelligence and the creation of microprocessors. This article will explore some of the most common light metal forming techniques and how they are used.
High Pressure Die Casting
Die casting is an extremely economical and high speed metal forming process which is advantageous as it can produce hundreds of thousands of castings quickly using just one mold. All of the components produced are uniform and it involves relatively low unit costs.
Die casting is an automated metal forming process which involves the liquid melt being pressed into a mold under high pressure (150 to 1200 bar) at a high filling speed. Alloys with low melting points are usually used and this casting process is used for mass production of components. Molds do not have to be destroyed after casting which makes them more economical than sand casting and it is possible to produce large and complex components with low wall thicknesses.
The most common use of high pressure die cast metal forming is in the production of components such as in casings and blocks, wheels, cylinder heads, manifolds and valve assemblies for the automotive industry. This metal forming technique is also used to cast parts that are used for power tools, furniture, electronics, aerospace, domestic appliances, and more.
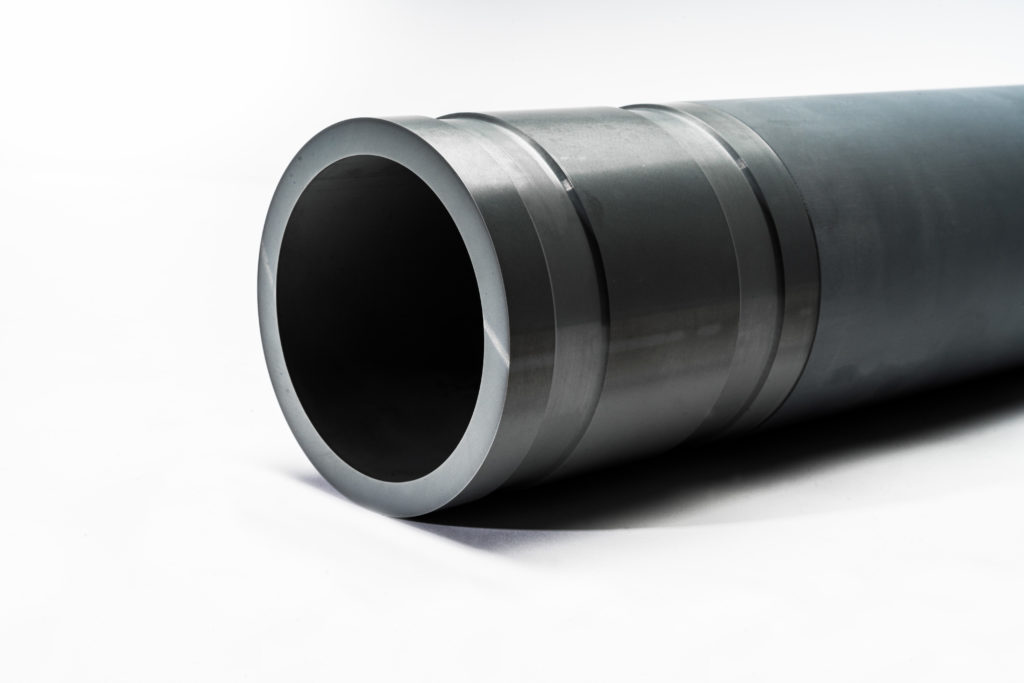
Extrusion
Metal extrusion is a metal forming manufacturing process which forces a softened cylindrical metal billet through a die of desired size and cross-section, in which the resulting parts are known as “extrudates”. These profiles or products, such as window frames, can be cut to length or move on to further processing including a series of extrusion and drawing steps to produce hollow tubes or wire.
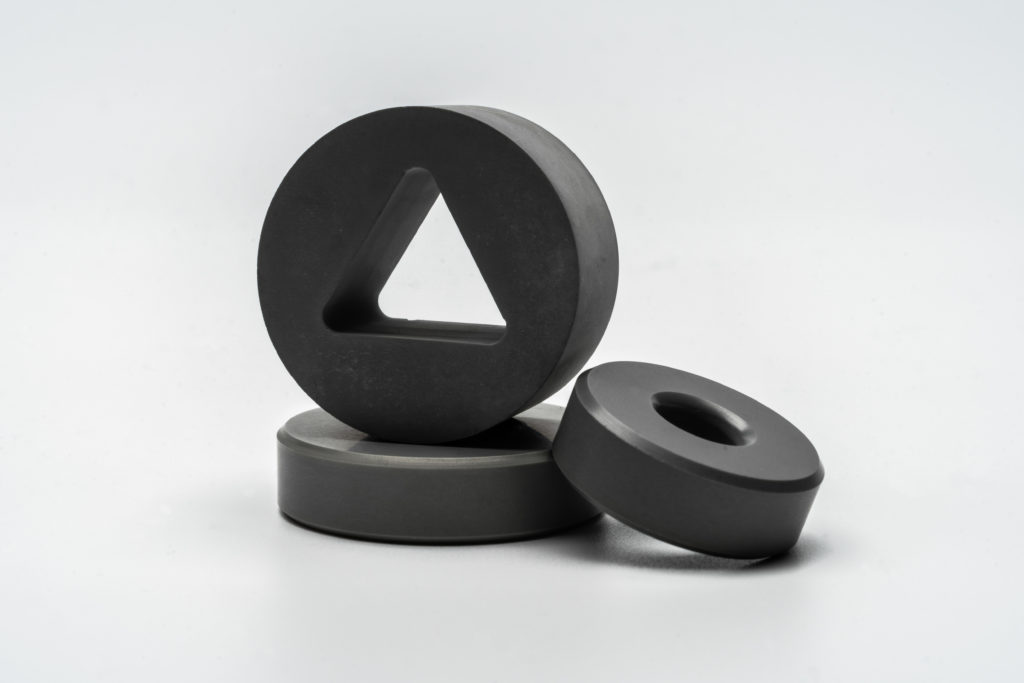
Rolling
Rolling is a metal forming process which involves metal being passed through one or more pairs of rolls to minimize thickness or make thickness uniform. Similarly to extrusion, the rolling process is usually a preform process from which final products such as food packaging or structural materials can be precisely cut and reformed.
Metal Forming Equipment from International Syalons
At International Syalons, we produce a variety of silicon nitride-based sialon and zirconia advanced ceramic components to be used in a range of metal forming applications such as casting, welding, extrusion and rolling.
Our Syalon 101 advanced ceramic extrusion dies, high-pressure riser tubes and rolling guides are the preferred option in industries where high strength, corrosion resistance and outstanding wear resistance are required.
At International Syalons, we manufacture advanced ceramic extrusion and drawing die inserts that can be shrink fitted into existing die casings and are used in extrusion and drawing of copper, brass, and nimonic alloys in the metal forming industry.
If you would like to find out more about how our products can be used in the metal forming industry, contact us today for more information.