Corrosion is the process by which a material deteriorates due to chemical interactions. All materials are subject to corrosive phenomena, but metals are especially prone to corrosion as surface atoms readily oxidise in specific conditions. There are steels designed to utilise oxidation for corrosion resistance (i.e. weathering steel) and other grades with regenerative patinas engineered to reduce surface corrosion (i.e. stainless steel). But few engineering-grade steels can match advanced, corrosion-resistant ceramics in terms of chemical stability.
This blog post will look at nine corrosion types affecting materials, most typically metal alloys.
What Types of Corrosion Affect Materials?
As corrosion is a severe problem across many industries, especially construction, it is essential to know the types and why they occur.
1. Environmental Cracking
Environmental cracking occurs as a result of environmental factors and therefore covers many conditions. This type of corrosion can cause a large amount of damage in a short period, and it includes corrosion fatigue, hydrogen embrittlement and stress corrosion cracking (SCC). Environmental cracking can be caused by different stresses that arise from processes such as heat treatment, residual cold work, or welding.
2. Erosion Corrosion
Erosion corrosion, a combination of erosion and corrosion on a surface, occurs when fast-moving, corrosive fluids wear down the surface of a metal.
3. Fretting Corrosion
Fretting corrosion occurs when two surfaces are continuously rubbed together during a process. Fretting and corrosion co-occur when materials are put under pressure during repeated action.
4. High-Temperature Corrosion
As the name suggests, this corrosion occurs under extreme temperatures (typically above 400oC / 750oF). High-temperature corrosion occurs due to a chemical attack from gases or molten metals. This commonly occurs in furnaces, gas turbines and machinery where hot gas contains specific contaminants.
5. Intergranular Corrosion
Intergranular corrosion is a form of localised corrosion which occurs at and around grain boundaries. The result is that the metal alloy is worn away and is reduced in strength.
6. Pitting Corrosion
Pitting corrosion is another type of localised corrosion that results in random small cavities or holes being created in a small area on the metal’s surface. This occurs when the protective oxide layer on the surface begins to break down, thus leaving the substrate vulnerable to corrosion.
7. Galvanic Corrosion
Often referred to as bimetallic corrosion, galvanic corrosion occurs when one metal preferentially corrodes another while contacting an electrolyte. Galvanic corrosion is most commonly associated with marine applications, where chlorides in seawater create pits in steel. However, it is also incredibly common in chemical manufacturing and molten metal handling. It chiefly occurs in ahighly acidic, alkali, and toxic environments, which can corrode through metals in a matter of weeks.
8. Fatigue Corrosion
Also known as stress corrosion cracking, corrosion and sustained tensile stress are applied to a material. Under high stress, the material’s boundaries begin to open, resulting in fine cracks along the surface.
9. Uniform Corrosion
This is typically the most common type of corrosion and refers to the process in which the entire material faces a corrosive attack. The whole surface area will be exposed to corrosion, and this commonly occurs to iron and steel when exposed to natural elements such as soil and water.
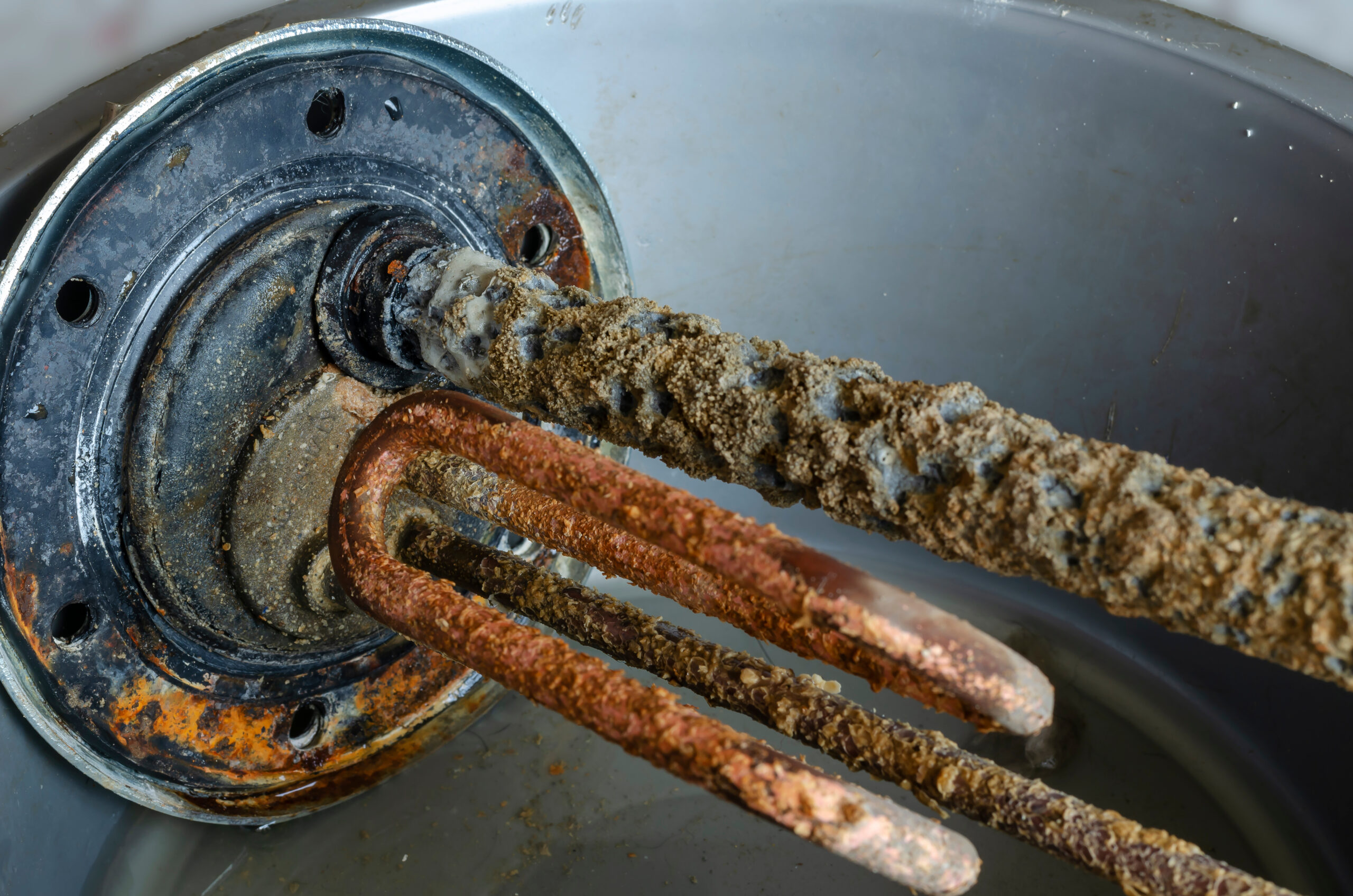
Corroded temperature sensor and heating element. Image Credit: Shutterstock.
Corrosion Resistant Materials with International Syalons
Corrosion is a common problem in many industries associated with heavy machinery and high-temperature processes. Corrosion-resistant ceramics play a crucial role here, as the most appropriate materials must be selected for your application to limit the risk of corrosion or eliminate it entirely in an ideal world.
Advanced ceramics are a key component in preventing industrial wear as they are highly corrosion-resistant materials. International Syalons supply a number of advanced ceramic materials that are ideal for use in many industrial applications.
If you would like more information on our advanced ceramic solutions, please get in touch with us today, and we’d be happy to assist you.