Update: Originally posted in 2022, this blog was updated with new context on 27/02/2024.
Wear and tear are familiar concepts. But the mechanisms of action underlying these phenomena can be surprisingly complex. Wear is defined as the loss of material from a solid’s surface due to mechanical action exerted by some other solid. It is such a universal process that only organic materials are immune since they can self-replicate and essentially restore surface fatigue. Therefore, every branch of materials science must contend with one or more different wear mechanisms.
Industry applications of wear testing cover a wide range of materials, from engineering plastics through to advanced wear-resistant ceramic materials like silicon carbide (SiC) and silicon nitride (Si3N4). Ceramic-lined components and systems designed for aggressive material handling are also routinely assessed for performance under dynamic wear conditions (i.e., for excellent wear resistance at high temperatures). Even the abrasive particles used for wear applications like cutting and grinding must be tested for optimal characteristics.
But what exactly is wear, and how are the different modes defined?
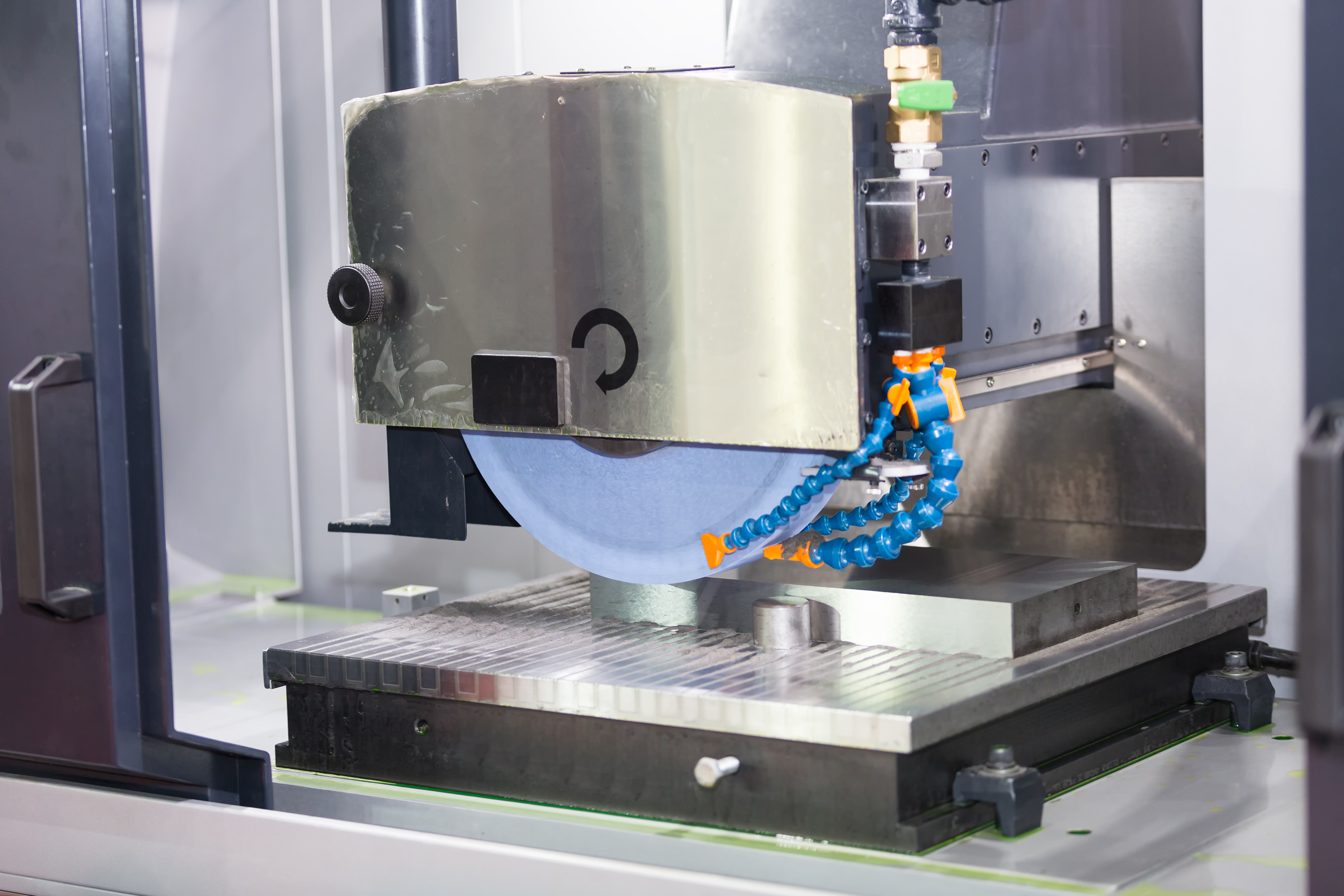
Understanding the Physics of Wearing
Though there are four overarching wear mechanisms, each is linked to frictional processes. Generally, frictional processes occur between contact surfaces which are in relative motion, causing the gradual loss of substance due to mechanical interactions and local deterioration at the interface. The main physical phenomena resulting in friction forces are shearing and ploughing.
- Shearing is defined as the opposing directional forces acting along the surface of a material; occurring when two contacting surfaces slide across one another.
- Ploughing, or plowing, occurs when the asperities of a harder surface cut into the surface along a softer one.
These are interlinked but separate phenomena which are both governed by the coefficient of friction (µ); a measure of the amount of friction between two surfaces.
What are the Different Wear Mechanisms?
Numerous factors contribute to the wear resistance of bulk materials, and numerous different modes of wearing. However, these can largely be categorised as one of four main mechanisms:
- Abrasive wear: The main mechanism of action used in industrial wear applications, abrasion occurs when hard asperities or protuberances on one surface are forced against another, and a velocity is applied. Estimates suggest abrasive wear is encountered in 36–58% of cases in industrial wear applications.
- Adhesive wear: Caused by localised molecular bonding, adhesive wear is characterised by particle transfer mechanisms between surfaces, and often occurs between poorly lubricated surfaces. Adhesive wear is less common than abrasion; being found in 23–45% of cases.
- Fatigue wear: Also described as surface fatigue, fatigue wear occurs when subsurface cracks appear due to fracture. Surface fatigue is encountered less frequently than the other two primary mechanisms of wearing: in approximately 14–15% of cases.
- Corrosive wear: Uniquely influenced by environmental factors, corrosion wear is the least common of the four main wear mechanisms; observed in just 4–5% of cases.
Numerous sub-categories exist, which may be described as wear modes. However, the distinction between a wear mode and a wear mechanism is poorly defined. The Encyclopedia Britannica agrees with the four basic types of wear outlined above, while ISO classifications suggest there are six main categories with fifteen subcategories. Yet it is easiest to differentiate the two classes mechanistically. Thus, there are four main mechanisms and various underlying modes, which include:
- Adhesion and transfer
- Cutting
- Plastic deformation
- Surface fracture
- Melting
- Electrochemical reactions
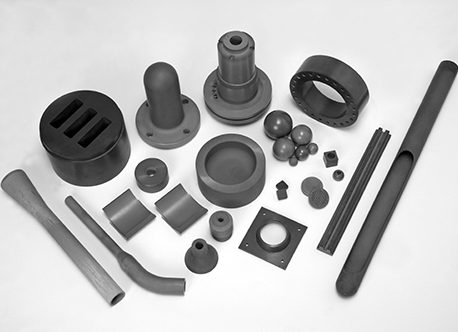
How to Measure Different Forms of Wear
There are various interlinked factors determining the wear rate of materials. Custom friction testing equipment is typically used to determine the amount of material lost from worn surfaces away relative to the duration and extent of contact between the workpiece and a tribological component. Essentially, a load is applied to a workpiece under set conditions to determine the wear resistance properties of the material in question. High-strength engineering materials are often assessed for abrasion resistance using scratch tests with extremely hard indenters.
Regardless of the test apparatus used to assess wear resistance, measuring surface deterioration from any mode is usually carried out via observation with microscopy, metallography, or radioactive isotope techniques.
A Deep Dive into the Wear Mechanisms of Ceramics
Wear mechanisms are extremely broad-ranging. What concerns the tribological properties of solid particles used for body abrasive wear applications may be inapplicable to tests designed to optimise the service life of a contact surface in machinery. It helps narrow the study scope to specific remits, such as the world of advanced ceramics.
Wear in Industry: Advanced Ceramic Case Studies
A study by K. Hokkirigawa (1991) focuses on the wear mechanisms of ceramics, categorizing them into three primary microscopic wear modes: flake formation, powder formation, and ploughing. These wear modes are critical to understanding how ceramic materials degrade under various conditions. The identification and analysis of these modes are based on in-situ observations of wear processes using a scanning electron microscope.
Flake Formation
Flake formation occurs when large pieces of material are removed from the surface, typically due to brittle fractures. This mode is often observed under conditions where there is high stress concentration at the contact points, leading to the initiation and propagation of cracks.
Powder Formation
Powder formation is characterized by the generation of fine particles as a result of wear. This mode is common in situations where there is less energy available for crack propagation, resulting in the material being worn down to small particles rather than larger flakes.
Ploughing
Ploughing involves the displacement of material without significant removal from the surface. In this mode, the material is deformed and pushed aside by the action of a harder material or asperity moving across its surface. This mode is less destructive than flake or powder formation but can lead to significant changes in surface morphology and texture.
The occurrence of each wear mode is theoretically analyzed using linear fracture mechanics. The analysis introduces two wear mode maps for ceramics based on dimensionless parameters Sc, S*c, and the coefficient of friction μ, where Sc is a function of maximum Hertzian contact pressure, maximum surface roughness, and fracture toughness, and S*c is a function of hardness, maximum surface roughness, and fracture toughness. These maps provide a framework for predicting which wear mode is likely to dominate under different loading and environmental conditions.
- The wear mode map using Sc and μ indicates the possible region for flake formation.
- The wear mode map using S*c and μ delineates the possible regions for powder formation and ploughing.
Experimental results for several ceramics under different conditions have shown good agreement with the predictions of these wear mode maps. This agreement underscores the practical utility of these maps in estimating abrasive wear resistance and understanding wear mode transitions in ceramic materials.
If you have found this article interesting and want to read more, refer to our industrial wear applications page for more details.
References:
- https://www.researchgate.net/file.PostFileLoader.html?id=559ed2cd60614b792f8b4580&assetKey=AS%3A273809964240908%401442292790888
- Hokkirigawa, K. (1991). Wear mode map of ceramics. Wear, 151, 19-228. https://doi.org/10.1016/0043-1648(91)90250-X.