Industrial processes are dictated by different, often conflicting, needs. Maximising throughput demands minimal downtime. But eliminating downtime is impossible when tools require maintenance to function at optimal levels. However, optimal functionality underlies desired yields and, of course, throughput. There is a cyclical nature to the demands of high-performance industrial components, but there is also a very clear throughline: maximising durability is critical to true quality assurance and profitability. Hence wear prevention is a critical factor impacting a wide range of end-to-end performance parameters.
This article will explore some of the basics of wear-resistant ceramic materials, and how technical ceramic components withstand different types of wear phenomena. Our goal is to show how you can reduce wear in challenging applications, including extremely high-temperature environments.
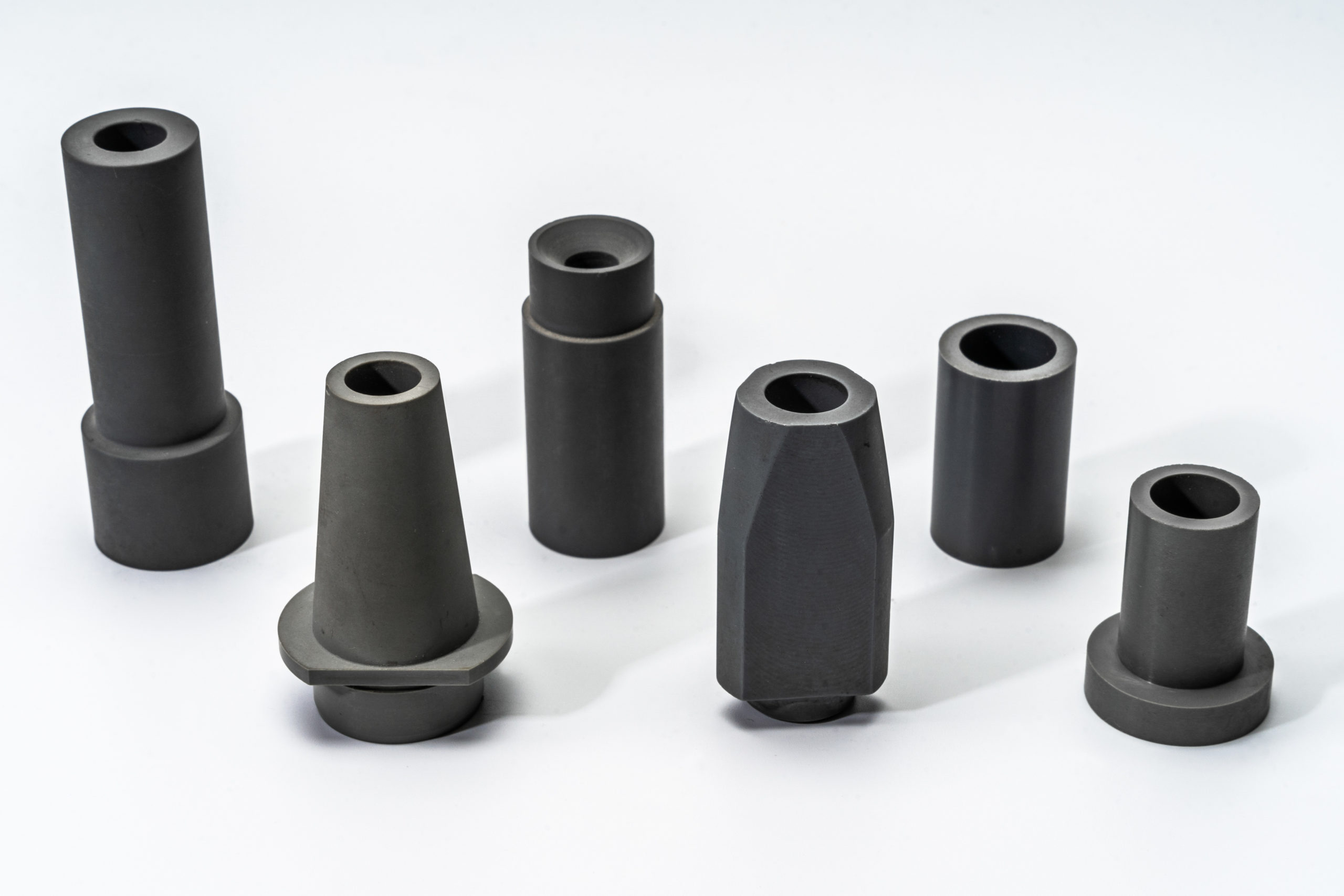
Why Use Advanced Ceramics for Wear Prevention?
Conventional manufacturing materials like tool steel and certain traditional ceramics often fall short of modern requirements. Today’s industrial systems operate at higher speeds than ever before, often contending with temperatures in excess of 1000C, extraordinary mechanical loads, and chemically aggressive media. This can lead to a raft of distinct wear mechanisms that inhibit functionality and, if left unchecked, may ultimately contribute to part failure. We discussed the various different wear modes in a recent article. Advanced ceramics are uniquely primed to resolve these issues.
Advanced ceramic materials such as aluminium oxide (Al2O3), silicon nitride (Si3N4), and zirconium oxide (ZrO) offer intrinsically high hardness, strength, and thermodynamic performance which yields an exceptional range of tribological properties.
Use the links in the table below for more detailed information about the specific thermomechanical properties of each material.
Aluminium oxide (Al2O3) | Aluminium oxide is one of the hardest advanced ceramics on earth with an approximate Vickers hardness rating of 15.71 – 17.65 GPa (Kg/mm2). This enables exceptional resistance to high abrading forces typical of wear applications. |
Silicon nitride (Si3N4) | Silicon nitride ceramic components boast a hardness of up to 19.81 GPa combined with superb toughness, making it a powerhouse for the most challenging wear applications (i.e. extrusion, weld locating). |
Zirconium dioxide (ZrO2) | Zirconium dioxide combines immense toughness with exceptional impact resistance and high-temperature performance, enabling it to withstand severe friction. |
Given that industrial wear is such a complex and dynamic phenomenon, optimal wear resistance is not denoted by an individual property. It requires intersectionality between critical parameters including hardness, toughness, and strength. Advanced ceramics eclipse traditional materials on virtually every one of these fronts, offering an ideal solution to various types of co-occurring wear modes.
A Quick Case Study in Advanced Ceramic Wear Prevention
Shot blast nozzles, for example, are continuously exposed to high-velocity abrasive media which may be chemically aggressive. Tungsten carbide (WC) is one of the most common engineering solutions for surface processing applications. However, despite their excellent density and mechanical strength, tungsten alloys still tend to succumb to microscale abrasive wear from minute abrasive grains. Advanced ceramic blasting nozzles based on a proprietary silicon nitride formulation have proven superior to tungsten components, allowing for more than 1000 hours of operation with chill cast-iron grit at pressures of 100 psi.
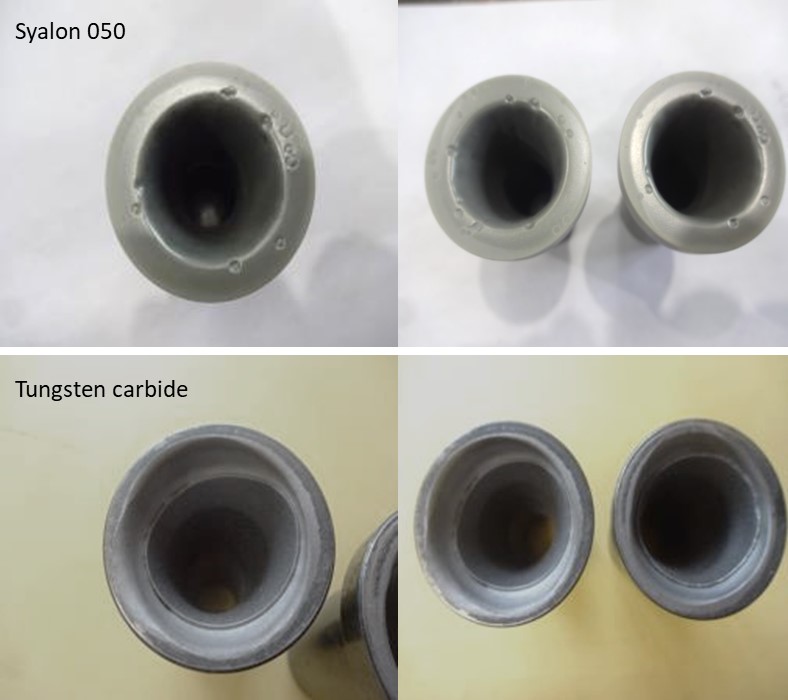
Looking to Prevent Wear in Your Process?
Integrating new high-performance materials into existing workflows can be technically challenging and will incur initial costs. That said, advanced ceramics provide the performance necessary for realising long-term cost-benefits associated with reduced downtime due to time-consuming, labour-intensive maintenance processes. Refer to our industrial wear applications page for more information about wear-resistant ceramics.