The properties of advanced ceramics make them extremely valuable in a wide range of industrial applications, like transportation, aerospace, and manufacturing. Most advanced ceramics are imbued with a crystalline or semi-crystalline structure, meaning they have improved thermal, electrical, and mechanical attributes. Moreover, advanced ceramics are specifically designed with a microstructural composition that is consistent to maintain the ceramic’s enhanced characteristics.
With so many useful properties, including wear and corrosion resistance, high temperature stability, and strength, advanced ceramic products are ideally suited to challenging conditions. This includes electronics and even nuclear reactors. The advanced ceramic property we, International Syalons, are going to focus on is their ability to withstand wear. By applying advanced ceramics to specific parts and components, for instance against corrosion or abrasives, their capability to enhance wear prevention can improve a product’s usability and overall length of life.
Below you will discover more about advanced ceramics and how they affect the wear of different products.
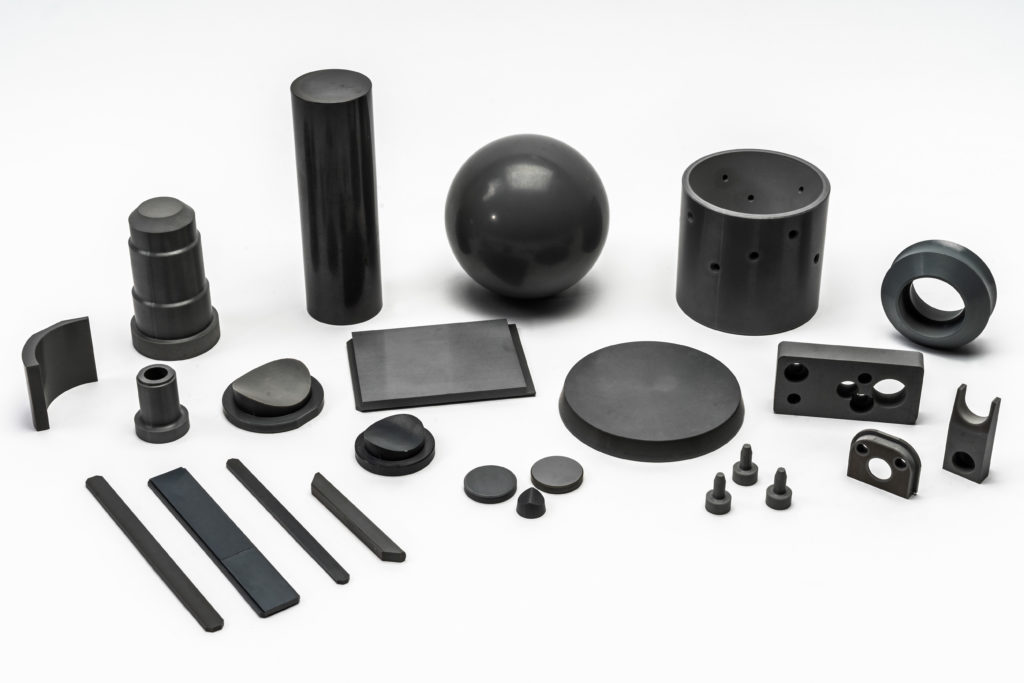
Why Use Advanced Ceramics for Wear Prevention?
Conventional manufacturing materials, like tool steel, tungsten carbide, diamond coatings, and traditional ceramics, often fall short of modern requirements. Today’s industrial systems operate at higher speeds than ever before. They often contend with:
- Temperatures in excess of 1000°C
- Extraordinary mechanical loads
- Chemically aggressive media.
This can lead to a raft of distinct wear mechanisms. Consequential results can include inhibited functionality and, if left unchecked, part failure. Advanced ceramics are uniquely primed to resolve these issues. We discussed various different wear modes in a recent article, so take a look at it if you want to learn more.
Advanced ceramic materials, such as aluminium oxide (Al2O3), silicon nitride (Si3N4), and zirconium dioxide (ZrO2), offer intrinsically high hardness, strength, and thermodynamic performance which yields an exceptional range of tribological properties.
Given that industrial wear is such a complex and dynamic phenomenon, optimal wear resistance is not denoted by an individual property. It requires intersectionality between critical parameters, including hardness, toughness, and strength. Advanced ceramics eclipse traditional materials on virtually every one of these fronts. They offer an ideal solution to various types of co-occurring wear modes.
A Quick Case Study in Advanced Ceramic Wear Prevention
Shot blast nozzles, for example, are continuously exposed to high-velocity abrasive media which may be chemically aggressive. Tungsten carbide (WC) is one of the most common engineering solutions for surface processing applications. However, despite their excellent density and mechanical strength, tungsten alloys still tend to succumb to microscale abrasive wear. This is from minute abrasive grains.
Advanced ceramic blasting nozzles based on a proprietary silicon nitride formulation have proven superior to tungsten components. They can allow for more than 1000 hours of operation with chill cast-iron grit at pressures of 100 psi.
Wear Prevention Can Be Achieved Thanks To The Attributes of Advanced Ceramics
Material science offers the opportunity to enhance advanced ceramics to ensure that their material properties and functionalities can suit a wide variety of applications. From applying this type of technical ceramic to the parts of a gas turbine, a device that requires components, like rotors and turbine blades, that can withstand heat, to using it within armor, the capabilities of advanced ceramics make it extremely versatile in its potential uses.
These ceramics have a large role to play in wear prevention because of their ability to withstand deterioration. This means that advanced ceramics can be used in a variety of settings that require wear prevention, including in:
- Machines: Extrusion dies, wire guides, and cutting devices
- Transportation: Turbochargers and systems for braking
- Power Creation: Heat exchangers and fuel cells
- Medicine: Implants in dentistry and joint replacements
When selecting a type of material for wear prevention, advanced ceramics should be one of your main considerations. Wear prevention is an attribute that could make all the difference in increasing the longevity of your products. For more information on wear prevention and advanced ceramics, we, International Syalons, invite you to read our industrial processing applications page. There you can learn more about advanced ceramics and their wear resistance, as well as the products we have to offer that incorporate this category of ceramic.