How do you decide between one engineering material and another? Cost is often one of the main influencers, but it is impossible to fully characterise integration and maintenance costs without fully understanding the material’s time-dependent performance under service conditions.
For instance, the relatively high cost of tungsten carbide (WC) is often justified by its incredible compressive strength—ranging up to 6,833 MPa — and wear resistance. However, high-temperature-driven plastic deformation of WC tools can cause losses of compressive strength. This reduced load-bearing capacity reduces effectiveness in high-stress applications and increases the likelihood of tool failure. Thus, a comparatively weaker material with greater temperature strength may yield longer service in specific applications.
Silicon carbide (SiC) is one of the go-to alternative ceramics when tungsten carbide is prohibitively expensive. However, it is increasingly used as the standard in applications requiring greater chemical and thermal resistance. Choosing between the two requires careful consideration of different extrinsic and intrinsic factors. Let’s explore some in depth.
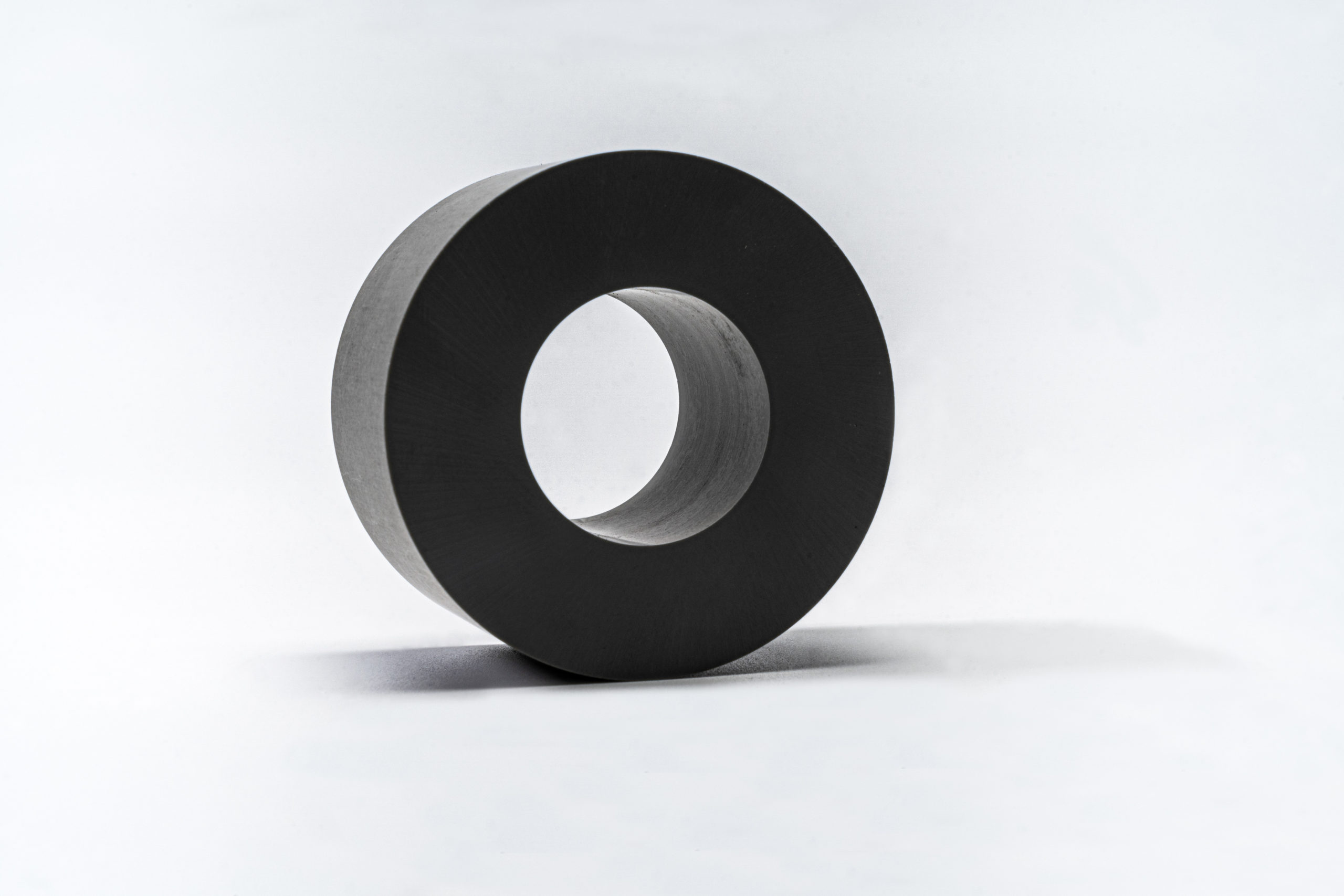
Silicon carbide bush. Image Credit: International Syalons (Newcastle) Ltd.
Abrasive Conditions
Hardness is a key characteristic for wear applications like cutting tools and grinding wheels. Silicon carbide, with a hardness of 9.5 on the Mohs scale, outperforms tungsten carbide, which has a hardness of 8.5-9. This higher hardness provides superior scratch resistance and wear durability, making SiC the preferred choice for abrasive conditions. Additionally, SiC’s lower density (3.21 g/cm³) compared to WC (15.6 g/cm³) ensures less mass-related wear and easier handling in high-speed applications.
Heavy Slurry and Extreme Pumping Conditions
Abrasion and corrosion resistance are crucial for heavy slurry applications or extreme pumping conditions. Silicon carbide excels in these areas due to its superior hardness and excellent corrosion resistance. SiC’s low coefficient of friction further enhances its performance by reducing energy loss and wear rate. Tungsten carbide, by contrast, is limited by its binder material. Cobalt-bonded WC, a common alloy, is vulnerable to strong acids. Enhancing the corrosion resistance of WC alloys using chromium or molybdenum additives is possible, but this further elevates material cost. Thus, silicon carbide is generally preferred for chemically aggressive environments.
High-Pressure Environments
Material strength and pressure resistance are paramount in high-pressure applications such as valve seals and wear-resistant coatings in oil and gas drilling. Tungsten carbide, with its higher density and superior strength, is more suitable for these conditions. WC’s ability to withstand substantial physical pressures and its high rigidity make it the material of choice for high-pressure environments. Although SiC also possesses high strength, its performance under extreme pressure conditions is generally outmatched by WC.
Rapid Temperature Changes
Applications associated with rapid temperature changes, such as furnace components and thermal barrier coatings, require materials with excellent thermal shock resistance. Silicon carbide is particularly well-suited for these applications due to its low coefficient of thermal expansion (4.0-4.5 x 10⁻⁶/°C) and high thermal conductivity (120-170 W/mK). These properties allow SiC to handle thermal stresses better than tungsten carbide, which has a higher coefficient of thermal expansion (5.0-6.0 x 10⁻⁶/°C) and lower thermal conductivity (84-100 W/mK).
Summary
Tungsten carbide is prized for its strength, toughness, and impact resistance, especially when cemented with nickel, making it indispensable in mining, construction, aerospace, and military sectors. However, in an era focused on cost efficiency, silicon carbide’s superior performance in high-wear, high-temperature, and corrosive environments offers significant benefits. While WC remains the go-to for general industrial applications due to its versatility, it’s worth considering if SiC could offer cost savings and efficiency improvements for your specific needs.
Discover the advantages of advanced engineering materials with International Syalons. Our expertise in silicon carbide and other high-performance ceramics can help you achieve superior efficiency and cost savings. Contact us today for a consultation and let our experts guide you in selecting the best material solutions.