Zirconia, or zirconium dioxide (ZrO2), is an advanced ceramic material which is used in a wide spectrum of applications, including abrasive and high-temperature processes, and in biomedical industries. This versatility comes down to the variable ZrO2 crystal structure. There are three disctint crystallographic phases of zirconia, and the properties of any given zirconia product depend upon which of those phases the material exists as.
- Cubic zirconia is the cubic crystalline phase of zirconium dioxide, forming at temperatures above 2370°C (4298°F). This material remains a competitor for diamonds due to its desirable optical and mechanical characteristics.
- Tetragonal crystalline zirconia forms at temperatures of 1170°C (2138°F) up to the lower threshold for the formation of cubic zirconia. Up to these temperatures, zirconia adopts a monoclinic crystal structure.
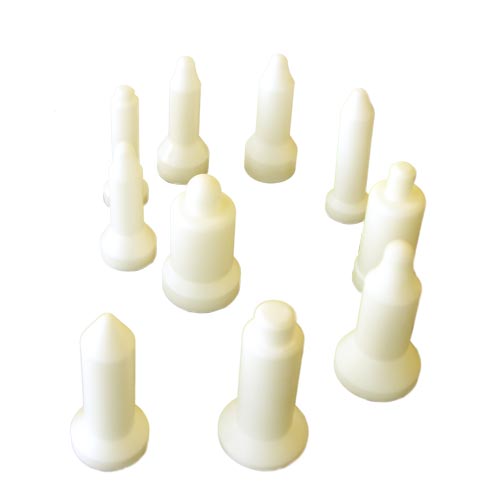
Engineered zirconium dioxide is typically doped with a stabilising agent such as yttrium oxide (Y2O3) to eliminate the risk of components undergoing phase transitions that can cause cracks and defects to propagate through the material. Yttria stabilised zirconia (YSZ) exhibits superior thermodynamic properties to un-doped zirconium dioxide due to its enhanced mechanical stability at varying temperatures. This not only reduces the risk of defect propagation but represents improvements to the ceramic’s thermal expansion and insulating properties.
What is Engineered Zirconia Used for?
Yttrium stabilised zirconia cannot compete with alternative engineered ceramics such as silicon nitride (Si3N4) or alumina (Al2O3) in terms of thermal resistance and stability. However, introducing yttria into the ceramic provides thermal stability at temperatures up to 1000°C (1832°F). Combined with the inherently high strength and impact resistance characteristics of zirconia, this improves the material’s longevity in abrasive applications with elevated temperatures. Weld location pins and captive nuts for sheet metal profiling are routinely manufactured using Zircalon ceramics. Beyond the industrial space, engineered zirconia is routinely used in dentistry, specifically for implants and veneers. Zirconia crowns are often preferred over porcelain counterparts for their greater stress-resistant properties.
Properties of Zirconia Products
The Zircalon range of zirconia ceramics is comprised of Zircalon 5, Zircalon 10, and Zircalon 20. These are amongst the toughest monolithic ceramics with outstanding impact resistance qualities at room temperature. Zircalon 5 and Zircalon 10 are not recommended for application in sectors where components are at risk of experiencing high thermal shock. However, they boast unmatched wear-resistant characteristics at ambient temperatures.
At room temperature, Zircalon 5 displays a modulus of rupture (MoR) of 1000 megapascals (MPa). Zircalon 10 meanwhile can withstand stress from bending at applied force values of up to 1200 MPa.
Learn More with an Insight Into the Hardness of Zirconia Ceramics
Zircalon 20 is a magnesium stabilised zirconia, representing significantly improved thermal shock resistance of ΔT = 350°C. Despite a drop in the ceramic’s MoR, Zircalon 20 still retains a compressive strength of up to 1600 MPa with outstanding impact resistance.
Zirconia Products from International Syalons
International Syalons is a leading supplier of advanced material solutions for demanding industrial applications. Our zirconia ceramics are engineered for wear-resistant applications with exceptional toughness and strength properties for withstanding abrasive influences. They are also suitable candidates for use in the chemical and process sector, with comprehensive chemical inertness in the presence of numerous concentrated acids at boiling temperatures.
If you would like any more information about our zirconia products, please do not hesitate to contact us.