Technical ceramics are among the most advantageous engineering materials ever developed, characterized by a diverse range of chemical, electrical, and thermomechanical properties. From hard-wearing silicon carbide (SiC) armour plates to piezoelectric zinc oxide (ZnO), components based on fine ceramic materials have permeated a broad range of market sectors. This far-reaching applicability stems from the compositional variety of ceramic compositions.
Though there are a myriad of custom ceramics available to manufacturers today, advanced ceramic materials typically fall under one of two overarching groups: Oxide or non-oxide. Aluminium oxide, or alumina (Al2O3), is the eponymous oxide ceramic from an engineering perspective, owing to its outstanding price-to-performance ratio and good all-round properties. Alumina is subsequently used throughout an incredibly broad application base. The non-oxide group is represented by technical ceramics that typically fulfil higher performance roles.
In this article, International Syalons will briefly explore two key non-oxide technical ceramics; sialons, and silicon carbide (SiC).
Sialons: Applications, Chemistry & Properties
Sialons are a novel group of technical ceramics based on the crystalline structure of silicon nitride (Si3N4). Despite exhibiting a comprehensive range of outstanding thermomechanical properties, the cost and difficulty of producing silicon nitride are often prohibitive. A novel alloy was developed by substituting some silicon for aluminium and nitrogen for oxygen, which yields the characteristic SiAlON alloy. The molecular arrangements of sialon ceramics are isostructural with silicon nitride albeit with improved thermomechanical performance. Sialons can also be more easily densified via liquid-phase sintering.
Read More: An Introduction to Silicon Nitride Ceramics
The comparative ease of fabrication and enhanced thermomechanical performance of sialons over silicon nitride technical ceramics opens numerous avenues of application for the alloy. Sialons now outperform so-called legacy materials in a range of wear- and temperature-resistance applications such as cutting tools, extrusion dies, molten metal handling, and welding technologies.
Want to learn more? Read our article sharing Design Tips for Silicon Nitride Ceramics
Silicon Carbide: Applications, Chemistry & Properties
A crystalline compound of silicon and carbon, silicon carbide was once the hardest engineered ceramic available, but manufacturing advances have since yielded technical ceramics like boron carbide (B4C) which eclipse SiC ceramics in terms of hardness. Despite this, with Vickers hardness ratings of up to 25.50 GPa, technical ceramic components based on sintered or reaction-bonded silicon carbide can withstand exceptional loads and impact forces.
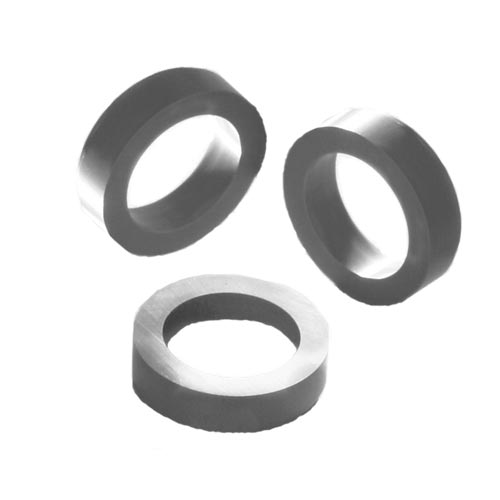
Today, silicon carbide ceramics are renowned more for their exceptional resistance to chemical attack by corrosive acids and alkalis alongside their superb thermodynamic properties. With excellent thermal conductivity and stability up to 1400°C (2552°F), silicon carbide is widely used to fabricate heating elements and mechanical seals for thermal processing and chemical applications.
Read More: Sialon Vs Silicon Carbide
Technical Ceramics from International Syalons
International Syalons is one of the UK’s foremost technical ceramic manufacturers, with a rich history in the design and development of advanced ceramic components for demanding areas of application. We offer a range of both sialons and silicon carbide technical ceramics for a broad market cross-section. For any more information, simply contact a member of the International Syalons team today.