Advanced ceramic grinding media are on the cutting-edge of wearing applications. The right grinding balls can be used to break down analytical samples, industrial intermediates, and more, simply by applying continuous abrasive forces. Generally, the goal is to reduce the size of particles, or to blend heterogeneous materials together. This can be carried out with hydraulic and pneumatic systems. But the oldest, simplest, and often most effective method, is to repeatedly impact sample materials with a tougher milling medium, causing particles to decompose through mechanical attrition.
Ball milling has been extensively used throughout history and it has emerged as one of the primary methods of production for metallic and ceramic powders with nano- and sub-micron scale particles and grain sizes. Typical ball mills comprise a cylindrical drum that revolves around a horizontal axis and is partially-filled with hard-wearing milling media. These spheres may be composed of any sufficiently high strength material, such as carbon steel, chrome steel, silicon carbide, tungsten carbide, and so on.
Sample materials are reduced by the continuous impacting action of the milling media as it falls from near the top of the drum. Rubber, stainless steel, and abrasion-resistant ceramics – such as silicon nitride (Si3N4) – are often used to fabricate milling media for industrial mixing or powder preparation.
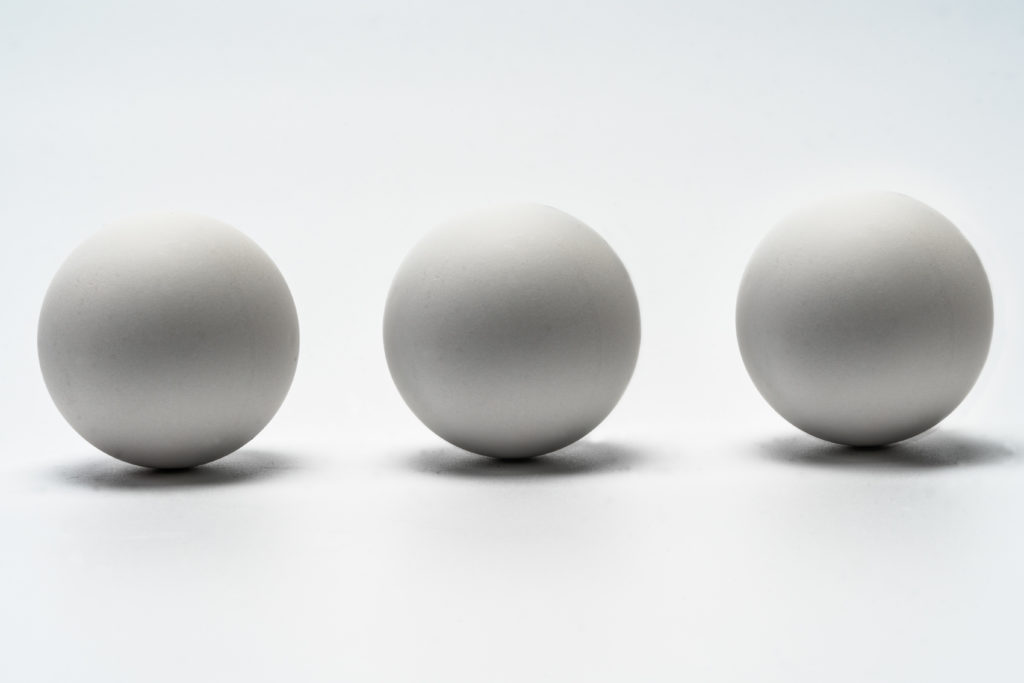
Drawbacks of Conventional Milling Media Materials
Conventional milling media such as rubber and stainless-steel balls display gradual degradation in hard-wearing applications, particularly when used to agitate samples down to very fine particle size distributions. Small particles can attack the grain boundaries of milling media and cause them to lose functionality over time. This can also result in the deposition of small volumes of undesirable material into sample batches, causing sample contamination.
Rubber balls are still broadly used to blend pyrotechnic powders and stainless-steel milling media remains something of an industrial standard for grinding minerals such as coal and feldspar. However, reducing samples down to functional nanoscale dimensions requires a more robust form of milling media.
Benefits of Silicon Nitride Milling Media
Silicon nitride is an extremely versatile material that can be formed into fully-densified spherical and pellet shapes through pressureless sintering. These ceramic balls represent extreme thermomechanical stability with highly tough grain boundaries, enabling them to resist fine particle abrasion and robust agitation within a revolving drum.
International Syalons engineers ceramic milling media from Syalon 101, a high functionality technical ceramic with outstanding strength and chemical resistivity properties. This material has also been used to develop linings for small mill pots or their internal shells. Studies have shown that silicon nitride sustains weight losses of just 14% compared to alternative technical materials under the same impacting and wearing conditions, which both reduces sample contamination and extends the service lives of both milling media and the lining of the ball mill itself.
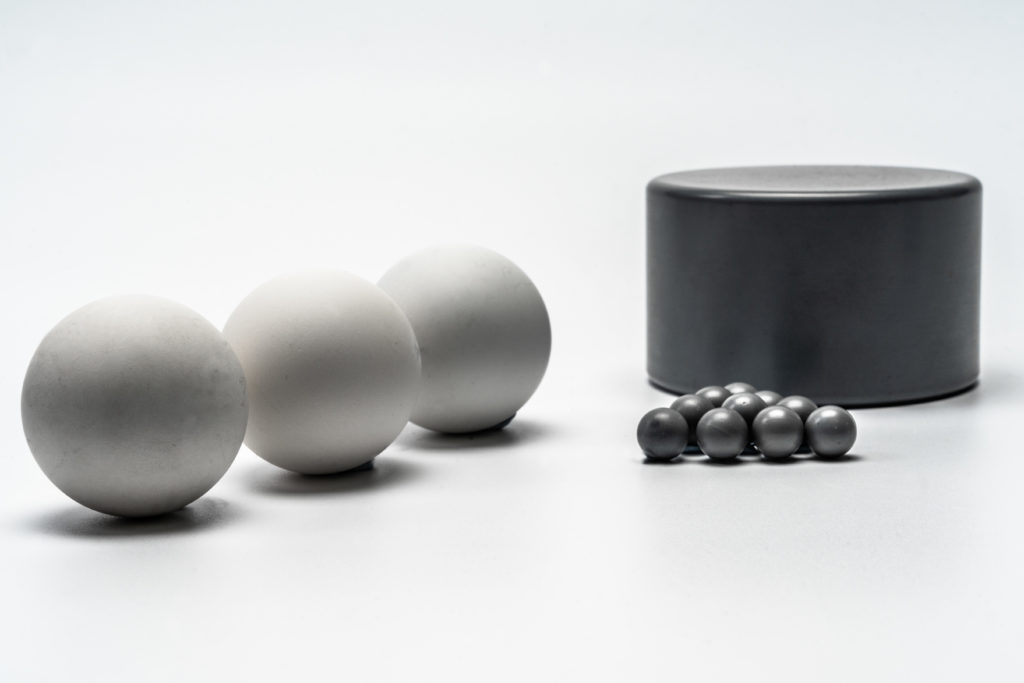
Looking for High-Performance Milling Media?
International Syalons has developed a robust family of silicon nitride materials suitable for hard-wearing applications, including mechanical grinding of intermediate powders such as pigments and catalysts. If you are struggling to choose a specific medium for your application, refer to our selection guide:
Selecting the Right Milling Media: Technical Ceramics or Steel?
Or, contact a member of the team today for more information about our products for grinding and industrial wear applications.