Lithographic additive manufacturing of advanced ceramics is an emergent technology that is unlikely to replace conventional bulk sintering and machining any time soon – if ever. This is due, primarily, to the scale and precision of components manufactured via 3D printing.
In this blog post, International Syalons explores the relationship between the use of novel lithographic additive manufacturing technology (L-AMT) of advanced ceramics and established traditional manufacturing techniques.
Ceramics Manufacturing: 3D Printing Vs. Isostatic Pressing
Advanced ceramics manufacturing via L-AMT can produce small, intricate components that are often proprietary or prototypical in nature. This technique uses a photocurable resin containing ceramic particles, and a precision light source that cures desired cross-sections of the material in sequential layers. Complex component designs with dimensions of just a few millimetres can now be realised without diminishing the exceptional thermomechanical properties of the parent ceramic.
Compare this to advanced ceramics manufacturing via a more conventional method such as isostatic pressing and green machining. Conventional manufacturing of ceramics for tolerances of within 1-3% can generally be produced ‘as-sintered’ via manual or CNC green machining of isostatically pressed stock billets. Dry-bag pressing is preferable for more complex components, requiring complex moulds to consolidate the raw materials into a desired shape before firing.
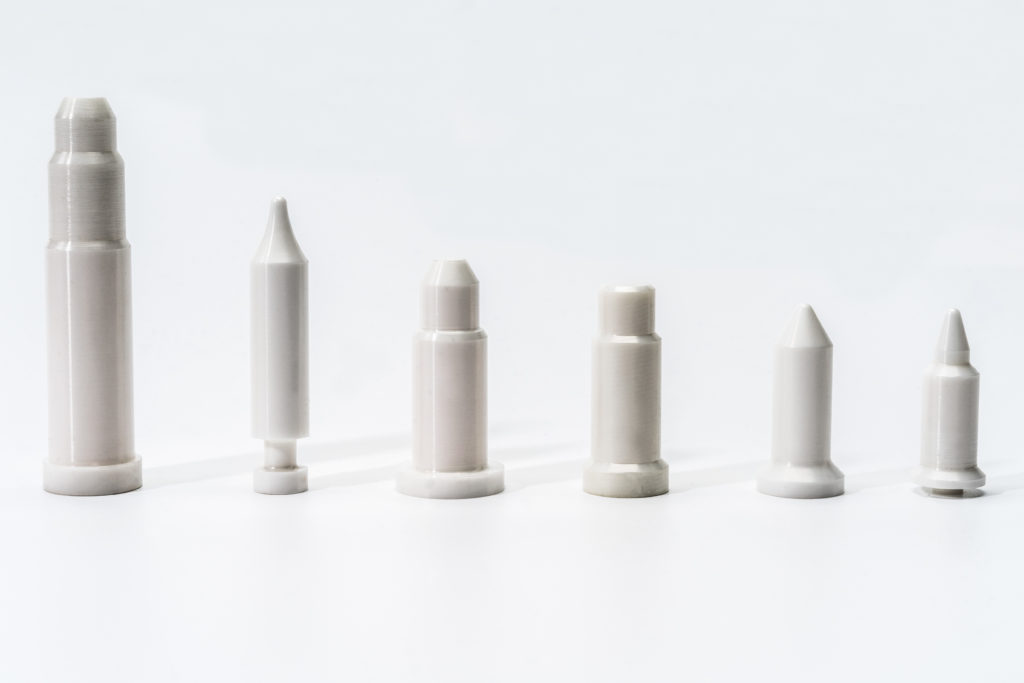
Although L-AMT ceramics manufacturing can be more precise and produce more complex parts than dry-bag pressing, its real-world applicability is still subject to debate. This is solely due to the immaturity of the technology, however. As it stands, 3D printing of technical ceramics is primarily suited for prototyping and unmachinable designs, which is already yielding appreciable cost-savings for engineers in the research and development (R&D) and design phases of numerous projects.
Syalon 101, a proprietary technical ceramic based on advanced silicon nitride (Si3N4), can be successfully deposited and cured into extremely complex profiles quicker than ever with L-AMT. In the past, Syalon 101 components would be formed through injection moulding, sintering, and subsequent diamond grinding; a costly and energy-intensive process. With 3D printing, smaller Syalon 101 components can be generated with rapid turnarounds, accelerating multiple design phases to help engineers perfect end-product performance.
L-AMT is a supplementary technology that is quietly revolutionising the capabilities of modern ceramics manufacturing. If you would like to learn more about the role they currently play in engineering sectors, read our previous blog post: 3D Printed Syalon Impellers for High Temperature Microturbines.
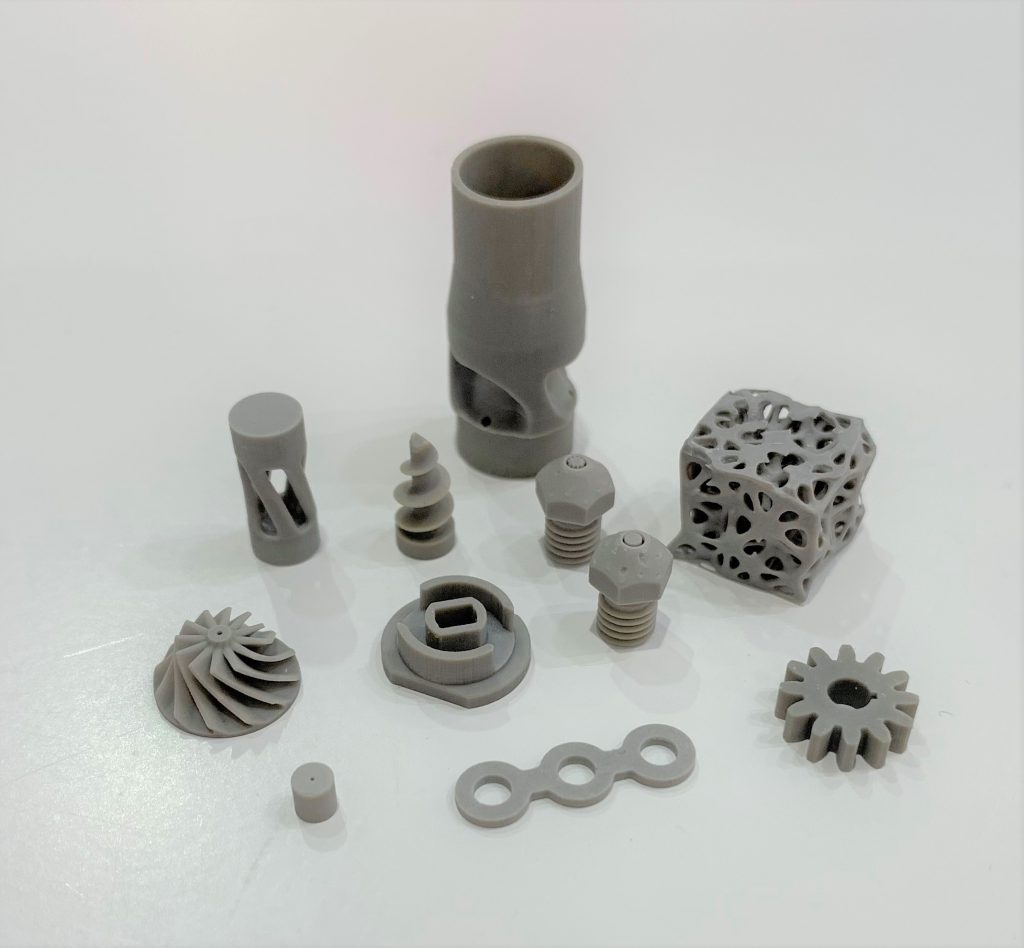
Advanced Ceramics Manufacturing with International Syalons
International Syalons is a world leader in the design and supply of advanced ceramics for every application. We have successfully used and optimised L-AMT with increasing real-world applicability and mechanical properties almost identical to the bulk material.
Read A Quick Intro to Additive Manufacturing Solutions
If you would like more information about our L-AMT capabilities, please do not hesitate to contact a member of the team directly.