Updated 11/11/21 to include the most accurate and up-to-date information.
Technical ceramics are ubiquitous in industrial manufacturing with a storied history of innovation and versatility. Manufacturers of some of the most hard-wearing and high-strength engineered ceramics worldwide are committed to pushing the envelope with regards to the capability of these novel materials. This has included fine-tuning the chemical composition of ceramic additives and raw materials to reduce the manufacturing costs of high-performance ceramics such as silicon nitride. All this, whilst still improving the material’s physical and thermal properties.
Recent innovations have included fabricating electrically conductive silicon nitride for electro-discharge machining (EDM), and developing high fracture toughness zirconia-based ceramics for demanding manufacturing processes. Yet, for many years, the industry at large has been focused on realising the potential of ceramic 3D printing.
What is Ceramic 3D Printing?
3D printing uses additive manufacturing (AM) to create geometries of potentially incredible intricacy and complexity, often building them layer by layer. It is now routinely used to fabricate high-quality components using a range of printing materials, including polymers, metals, and even biological material for both novel and well-established applications. AM technologies are even used for complex biopharmaceutical processes like vaccine development. Yet 3D printing of ceramics has historically remained elusive due to the inherent challenges of ceramic manufacture.
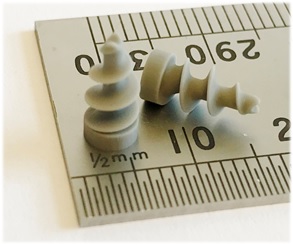
Developments in Additive Manufacturing of Ceramics
The 2015-2017 European Commission funded Horizon 2020 ToMax project (Toolless Manufacturing of Complex Structures), made huge progress in realising the potential of lithographic additive manufacturing (L-AMT) for ceramic materials.
International Syalons were a consortium member of the project. We have since had significant success in the manufacture of silicon nitride ceramic parts. These feature identical thermomechanical properties to those of components produced via conventional routes, such as pressing or extrusion. Introducing additive manufacturing for silicon nitride ceramics enabled us to supplement conventional silicon nitrides with new prototype technologies and smaller-scale components.

SEM image showing a cross-section of L-AMT Syalon 101, and fracture surface comparison for L-AMT and conventionally manufactured Syalon 101.
3D printing of ceramics is still an emergent technology, however, the industry has made great advances towards the commercialisation of additively manufactured ceramic components. Manufacturers of ceramic 3D printers, like Lithoz GmbH, 3DCeram Sinto, Admatec BV, ExOne, and XJet can confidently supply equipment and feedstock materials for both rapid prototyping and serial production. This includes manufacturing of non-oxide advanced ceramics, and most are developing technologies for non-oxide ceramics such as silicon nitride, silicon carbide, and CMCs.
Lithographic-based systems are often considered the most suitable manufacturing method for highly complex and precise geometries with optimum mechanical properties. This printing process is also desirable as it yields finely toleranced parts with minimal post-process requirements. Whilst binder jet or extrusion type systems offer the greatest potential for large volume components or low-cost production.
As an industry, 3D printed ceramics could be worth more than $3 billion globally. But there are several factors inhibiting market growth. Namely, the high cost of equipment and 3D printing materials, which must often be purchased from the same supplier.
It is well appreciated across the ceramic industry that AM technology will not replace conventional production methods, but will instead complement existing technologies to broaden capabilities.
3D Printing Ceramics with International Syalons
International Syalons continue to work closely with leading L-AMT system manufacturers and are committed to developing high quality 3D printed silicon nitride-based components. To find out more about our materials and these technologies, contact us today.
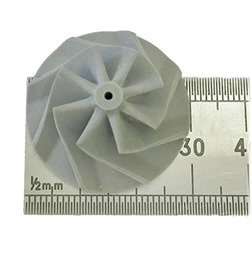